Kraig Biocraft Laboratories, Inc. (KBLB)
To our knowledge, Kraig Labs is the only company producing recombinant spider silk fibers. While the companies identified below could be considered competitors in the broader space of designer protein-based polymers, one by one, each has dropped the term spider silk from their product descriptions and marketing, and none, to our knowledge, are even claiming to produce continuous recombinant spider silk fibers.
Therefore, we have described the companies listed below as potential competitors.
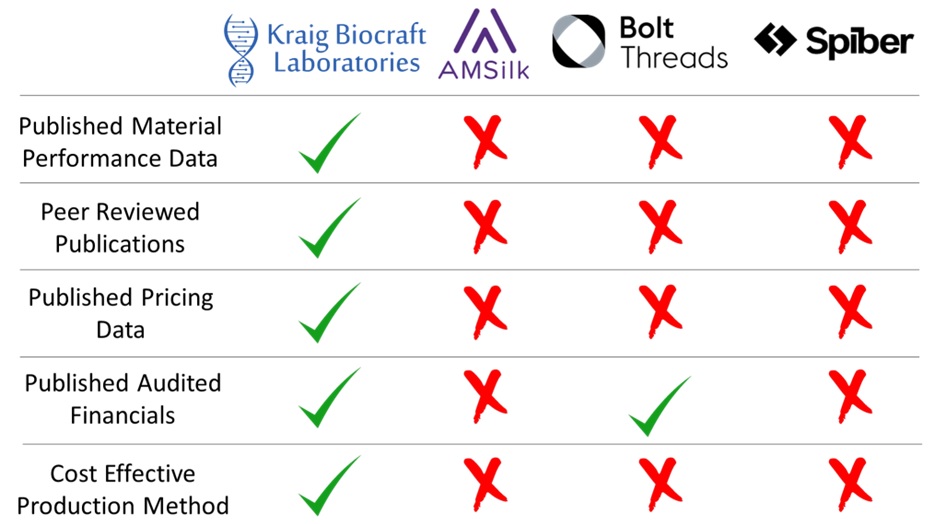
As demonstrated by the table above, we believe that Kraig Labs is the most open and transparent company operating in the spider silk industry.
When Kim Thompson first launched Kraig Labs, very few people believed a scalable spider silk production platform could be developed. As Kraig Labs has proven the feasibility of producing spider silk, industry is beginning to see the tremendous market potential for the product, and well-financed competitors have entered our field. That is a natural development in a field like technical textiles, where billions of dollars are at stake.
We accept the entry of competitors as verification of our own analysis of the market. As the world leader in this technology[1], we note that others stood by while we cleared the land, plowed the field, and did the heavy lifting. When we look at those attempting to compete in this market space, we are reminded that imitation is the height of flattery.
As we look at the very large investments made by venture capitalists into the development of rival technologies, we cannot help but smile. They have discovered what we have known for some time: recombinant spider silk has the potential to make significant inroads into the multibillion-dollar textile and technical textile industries, opening up new avenues of human innovation.
Some of the attempts to compete with our little Company, in at least one case, by pushing hundreds of millions of dollars into a poorly designed venture, are hard to comprehend.
As an example, Bolt Projects Holdings (formerly Bolt Thread) was founded with substantial venture capital money to produce spider silk. After years of work and undisclosed millions spent, Bolt sidelined its attempts to produce spider silk and instead switched its business model to the development of fungi-based artificial leather.
After additional years of research and having spent more than an estimated $200M in combined research and development, Bolt “paused” its artificial leather business. It then U turned its business model once more. This time to the production of a powdered protein it calls “B-Silk.” Bolt does not claim to be producing spider silk fibers. We have no reason to believe that it is producing or attempting to produce any fibers.
As of this date, Bolt has turned an estimated $350M investment from San Francisco-based venture capital firms into a $9M market cap. As of this writing, Bolt is subject to a NASDAQ notice to cure its market cap deficiency or be subject to delisting. We no longer view Bolt’s management as serious competition in the field of spider silk-based fibers. Nevertheless, for purposes of disclosure, they are listed here as a potential competitor.
Kraig Labs has always believed that we have a superior technology and product. We are both proud and humbled that our little firm has taken a leadership role in this industry, and in the coming year, we intend to significantly increase the gap between Kraig Labs and its nearest potential competitor.
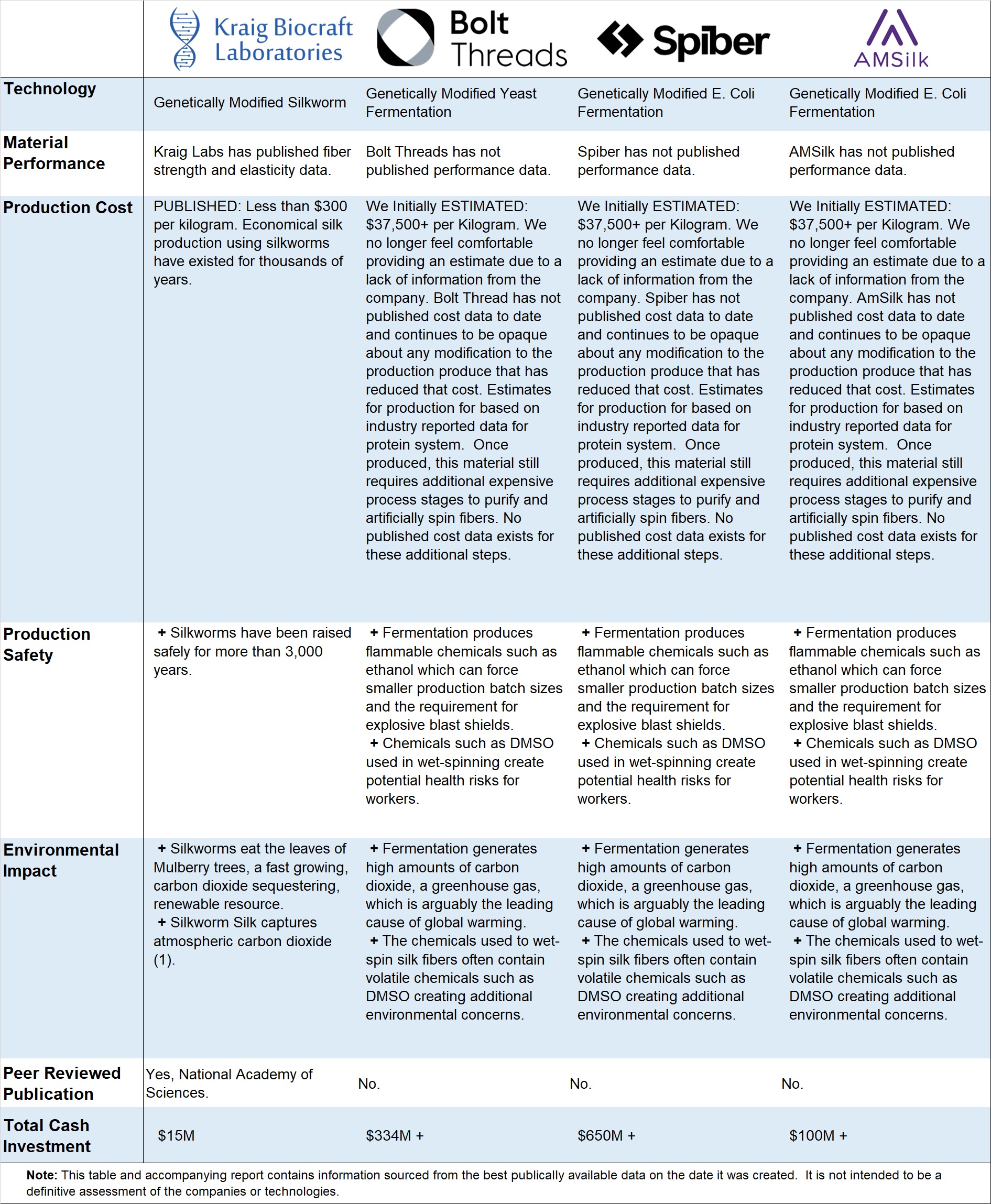
Table References
- pubs.acs.org/doi/abs/10.1021/bm0340063?journalCode=bomaf6
- www.thelocal.de/20110913/37547
- www.bloomberg.com/news/features/2016-05-10/japanese-spider-man-hopes-to-spin-startup-gold-from-artificial-silk
By the Numbers
Venture capital money has poured into spider silk technology, and there has been more than $1.3 billion in total investment to date. However, Kraig Labs, with its minimal cash investment, continues to remain a standout market leader in the space.
Bolt Projects Holdings has publicly reported more than $334 million of investment capital leading up to its IPO in late 2024. They have turned that $330+ million dollar investment into a $9 million market capitalization, with more than $13 million in debt overhang and, with it, a notice to cure or face delisting from Nasdaq.
Spiber remains a privately held company with more than $650 million of capital raised. Their technology is based upon genetically modified yeast fermentation. Spiber does not claim to be making spider silk but they are making some form of designer protein. They have made no public disclosure regarding sales.
Amsilk’s most recent capital raise was $23M in 2023. They remain private and have no publicly reported sales. Their technology is based upon genetically modified e-coli bacteria. In 2019, they sold their cosmetics business to Givaudan for an undisclosed amount.
Material Performance
Kraig Labs is the only recombinant spider silk producer to publicly provide performance specifications on our recombinant spider silk’s strength and elasticity.
Our potential competitors have yet to publish strength and elasticity data for their products in development.
Kraig Labs is committed to sharing measurable results with our shareholders and the public.
Production Techniques and Cost
Kraig Labs’ genetically modified silkworms are incredibly efficient and proficient recombinant spider silk producers.
Why silkworms? Because silkworms have a proven industrial-scale production record, they generate roughly $20 billion in total sales per year. Our technology simply harnesses that production capacity by introducing a genetically engineered silkworm that produces recombinant spider silk instead of mundane silk. The result is a scalable and incredibly cost-effective process.
Our potential competitors, who have attracted some press and the interest of venture capital over the last few years, are using a very different technology. They are genetically engineering yeast and bacteria to excrete protein into the soup that they live in. While it may sound simple, the fermentation of recombinant proteins is neither simple nor, in our opinion, cost-effective.
In this fermentation process, microorganisms are grown in bulk in a growth medium with the goal of producing a specific chemical product. However, unlike beer fermentation, recombinant protein synthesis requires a number of additional production steps and potentially hazardous chemicals. These requirements increase costs and raise safety implications. For instance, fermentation produces high quantities of combustible chemicals, like ethanol, which limits batch size and requires expensive safety measures in order to reduce the likelihood of explosions or fires.
Perhaps the reason our competition is uncomfortable releasing cost data is because fermentation production costs are high. While we no longer feel comfortable making any estimates of their costs due to the complete lack of data and transparency, our early estimates, sourced from multiple independent protein production firms indicated that a 1,000 liter batch of GMO yeast or bacteria used to excrete recombinant protein could cost anywhere from $700,000 to $1,000,000 to produce and manage. At a high protein yield of 20 grams of usable silk protein per liter of solution, this could cost anywhere from $35,000 to $50,000 per kilogram of silk protein.[2] These costs do not include the cost of other items and processes, like silk protein purification and wet-spinning the protein globs. These additional steps are all required further down the production process before you ever get to usable silk fibers.
Following fermentation, the next critical steps in the creation of silk from that process are extracting the protein from solution and drawing it into synthetic silk fibers. The recombinant proteins must go through a purification process and then must be “wet-spun” to produce usable fibers. Wet-spinning is a process that typically requires the use of controlled chemicals like dimethyl sulfoxide, or DMSO, which must be handled with extreme care. These steps not only add time, but significant upfront cost to the process as well.
Unlike our competitors, Kraig Labs works with nature’s own silk production factory, the silkworm. While others believed it could not be done, we overcame the technical obstacles and created several lines of genetically modified silkworms which spin recombinant spider silks. Our work in the laboratory has produced a practical and elegant production platform which is inherently cost-effective.
Instead of using a complex fermentation, purification, and wet-spinning system, we let nature do the work for us. Our genetically engineered silkworms are raised using the tried and true methods used by silk farmers for millennia. Our production process is as simple as growing and feeding white mulberry leaves to our proprietary silkworms and harvesting recombinant spider silk directly from the cocoons. Using this economical technique, our recombinant silk production can decisively beat the $300 per kilogram[3] threshold.
Environmental Impact
While being environmentally conscious is the objective of all producers in this industry, the fermentation process produces high levels of carbon dioxide. In stark contrast, Kraig Labs’ mulberry trees and the silk from silkworms have proven to be effective at sequestering carbon dioxide and are renewable resources. Mulberry trees are also very low maintenance while still providing essential global green cover and significantly help in reducing soil erosion.
In addition to potential climate impacts of the fermentation approach, solvents typically used to wet-spin fibers can have significant environmental impacts. DMSO, one of the materials mentioned previously, can be absorbed directly through human skin, carrying with it potentially dangerous side effects.
The Market
The global market demand for technical fibers is growing rapidly as the products have become essential for industrial and consumer applications. In 2024, the global market for technical fibers reached approximately $206 billion. The demand for technical fibers is expected to reach $340 billion in 2032. As an example, in 2024, Du Pont’s segment sales in this market (with its products Kevlar®, Tyvek® Typar®, Nomex®, and Sontara® are estimated at $5.4 billion. In addition to the performance and technical fibers markets, the Company is targeting the multibillion-dollar silk market. The market for raw silk fibers alone is a $19 billion market.
The potential applications for spider silk products include the following textile markets:
- Medical textiles
- Geotextiles
- Textiles used in Defense and Military
- Safe and Protective Clothing
- Filtration Textiles
- Textiles used in Transportation
- Textiles used in Buildings
- Composites with Textile Structure
- Functional and Supportive Textiles
- Performance Sportswear
- Traditional Fashion Apparel
The Company believes that the superior mechanical characteristics of the next generation of protein-based polymers will open up new applications for the technology outside of traditional textiles and result in a significant increase in demand. These fibers can justifiably be referred to as “super fibers.”
In addition to spider silk’s potential anti-ballistic and textile qualities, spider silk’s amazing properties could make it the basis of many market-disrupting technologies in industrial, military, and consumer applications, requiring superior strength, toughness, and flexibility. Beyond traditional fiber properties, recent discoveries in the ongoing study of spider silk have identified a number of truly amazing properties, including the ability of spider silk to function as a fiber optic chemical sensor.[4]
In Conclusion
Kraig Labs is delighted that we have achieved scientific and technological breakthroughs with brainpower and ingenuity, and not by throwing money at a dart board. The result is our unparalleled technical prowess and process advantages. Unlike our prospective competitors, who jointly invested more than $1 billion, Kraig Labs used minimal cash (roughly $14 million) and a considerable amount of sweat equity and brain power.
Kraig Biocraft Laboratories (KBLB) is the only company in this space to subject our scientific work to the peer review process and publish with the National Academy of Sciences. That is because we are confident in our work and our results. We are the only company in this competitive space to publicly report our material performance specifications. We are the only company to disclose our production cost structure.
We are proud of the achievements, both in the lab and in the field, that have made us, arguably, the world leader in spider silk technologies. We intend to maintain and expand that position of leadership in this new spider silk industry. As the world leader in recombinant textiles, we believe we are poised for success in the technical textiles marketplace.
[1] Www.kraiglabs.com/world-leader/
[2] Multiple independent protein fermentation providers provided these cost estimates. These estimates reflected the cost for usable silk protein on a per kilogram basis as of that time.
[3] Our production cost advantage appears to be of an order of magnitude when compared to “fermentation” based technologies.
[4] https://phys.org/news/2022-08-biosensor-spider-silk-optical-fiber.html#google_vignette